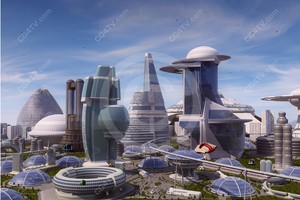
3D Printing is taking fashion by a storm! What lawyers need to know
Craftsmanship and handiwork is not necessarily eliminated with the advent of 3D technology and a sea change is coming to luxury brands in particular. Initially, fashion brands were quite skeptical about 3D printing, likening it to a copy machine on steroids and not a technology that can produce items to which a designer can feel proud or a consumer can feel luxe. While Chanel has just announced its embrace of 3D printing in its July, 2015 Paris fashion show by showcasing tweed jackets that were created using the technology, it is not the first brand to use 3D printing to fashion (pun intended!) some terrific wares. Currently, fashion brands are learning about the technology in order to determine whether to strategically use it or to reject it.
3D printing is an additive technology which creates three-dimensional objects by laying thin layers atop each other; in fashion, traditionally melting or laser sintering is utilized. Melting technology is simple – metals (e.g., silver and gold) are melted and then layered to form an object such as a ring or necklace charm. When you watch the layering process, you can think of the old typewriter heads that moved left to right when typing and right to left to start a new line. It is the same here. The machine moves from left to right until an item is stacked into form. Laser sintering technology allows users to cut into materials to create a type of lattice work or allows you to cut into an already formed object (e.g., acrylic or plastic) to form another object such as a necklace or bracelet charm.
Consumers are buying several 3D printed pieces but are unaware of how the item is being manufactured. Since 3D printing within fashion is in a relatively early stage, many designers and brands are not advertising their use of the technology.
One of the challenges with the technology is quality control. For example, if something does not print properly, is it the designer’s vision, the 3D printer, the software that drives the machine or something else? At this experimentation phase, it is a liability touch and go. As such, as attorneys representing fashion brands, designers, etc., we should explore contractual provisions that mandate collaboration rather than simply shift risks.
Usually, when creating or reviewing contracts we focus on culpability and cure periods; instead, due to the newness of the technology, we should emphasize teamwork (all parties work together to determine what tweaks are necessary to properly produce the item in question) and collaboration. In other words, until all parties are comfortable, think of those involved as part of your team. Some provisions that you may want to consider including in your collaboration contract are:
- The number of adjustments included in the total project cost;
- The cost of each, additional adjustment;
- Whether the adjustment includes alternative materials (different metals, plastics, or textiles); and
- Production time extensions necessitated by adjustments.
For example, several designers are hiring architects to help them effectuate their vision. Architects, as you may know, have used AutoCAD, which is similar to 3D printing, as it models 3D objects. With the knowhow of the architects and the aesthetic eye of the designer, 3D printing will allow artisanal work to go to an entirely new level and 3D technology will permit designers to create pieces that they couldn’t before because their vision may have been too complicated to create without the 3D technology. =Once accepted fully, designers will have unlimited possibilities for creating one-of-a-kind couture items for which they can charge an even higher price.
The result will likely be that companies who do not embrace the technology will be left behind as the technology upends manufacturing and the fashion supply chain as we know it today. Until the next article, consider this: what will the supply chain look like when manufacturing plants and warehouses are full of 3D printers rather than seamstresses? What will the new fashion Ateliers look like? Do you believe that the bespoke tailor will take your measurements using measuring tape? And, what types of textiles will you be wearing five or ten years from today? One thing is for certain. Change is here and is constantly evolving. Will your brand become a thought leader, a follower or a contrarian?
Source:
http://www.insidecounsel.com/2015/08/04/3d-printing-and-fashion-how-the-tech-is-being-used?page=2
Kommentare
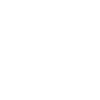