
If you believe Tesla, affordable, long-range electric cars could be here sooner than many think. I recently took a test drive in one of Tesla’s luxurious Model S electric cars and toured its R&D labs, where it’s developing its battery and recharging technology. The experience left me believing that Tesla has an important edge over its competitors in the race to bring electric cars to the masses.
Tesla’s Model S is expensive (it ranges from $70,000 to over $100,000), but its range is 265 miles, more than triple that of Nissan’s Leaf (75 miles). Within a few years, Tesla hopes to produce much more affordable vehicles—including one that costs $30,000 to $35,000—with a range similar to that of the Model S. Tesla also wants to make electric cars more practical by building a nationwide network of charging stations that can deliver 200 miles of charge in about half an hour—compared to several hours to charge an electric car at an ordinary station today.
For the test drive, I planned a drive from Tesla’s headquarters in Palo Alto, California, into San Francisco, then over to Half Moon Bay for a cruise down the scenic coastal Highway 1 to Santa Cruz. Later, I’d head back north to Fremont for a Tesla factory tour, before returning the car to headquarters—the whole trip would add up to about 230 miles.
When I got to Tesla in Palo Alto to pick up the car, however, I discovered that someone had forgotten to plug it in overnight. The battery gauge read 208 miles—short of the full 265-mile range for the Model S. I could still make my trip, but a stop at a supercharging station was now essential.
Today’s electric vehicles promise several advantages over gas-powered cars. For commuters, there are no trips to the gas station—all you need is an outlet at home or work—and a full charge only costs a couple of dollars. And electric motors, which need only a single gear for all speeds, can also be surprisingly responsive and powerful. What’s more, electric cars use no gasoline and emit no pollution. Even when you factor in the carbon emissions and pollution from the power plants that produce the electricity to power the cars, and from manufacturing and disposal, electric cars produce about 40 percent less carbon dioxide and ozone than conventional cars.
But for all their attributes, electric cars still are haunted by two damning factors: high costs and less-than-optimal batteries.
That’s where Tesla hopes to make a difference. The company’s innovative battery and charging technology has given it a substantial lead in making batteries cheaper and recharging quicker, and it’s also helping Tesla lower costs faster than its competitors.
At about 10 a.m., I drove out of Tesla’s parking lot, taking advantage of the car’s acceleration—0 to 30 in 1.7 seconds. Throughout the day I passed other cars while climbing steep hills, took curves at speed, and left other cars standing at stoplights.

Fuel gauge: The Model S’s dashboard shows current position, remaining charge, and energy consumption over time. The part of the rightmost chart in green shows the result of regenerative braking.
But I felt a twinge of anxiety when I noticed just 67 miles of charge left in the battery. The car estimated that I’d arrive at the closest charging station, in Gilroy, with 20 miles to spare—about half what I’d expected to see. I wouldn’t have been worried if I knew I could count on that estimate, but as with any electric car, the actual range varies depending on your driving style, the terrain, and traffic. The Model S shows two different range estimates: one that ticks down gradually, like a fuel gauge, and another that shows how your range would be affected if you kept driving like you have been for the last few minutes. I turned down the air conditioning, dimmed the car’s huge 17-inch touch screen, and eased off the accelerator to conserve some juice. I arrived with 17 miles left in the battery.
Recharging was far easier than I’d expected, having once spent an afternoon charging a Chevrolet Volt at a standard public charging station to get just 30 miles of charge. The car recognized an RFID tag in the charger handle and automatically popped open the outlet door. By the time I’d walked across the parking lot, bought a cheeseburger, and carried it back to the car, the range was already up to 92 miles, plenty to finish the day’s driving. I chatted with a Model S owner for a while and then got back on the road. I returned the car that evening with 129 miles of range left in the battery—more than the fully charged range of battery-electric cars from Toyota, Nissan, Ford, GM, Honda, Fiat, Renault, Mitsubishi, Smart, or Scion, or upcoming electric cars from Mercedes and BMW.
Despite the compelling advances, the same challenges for electric cars remain: cost and range. Because superchargers aren’t on every corner (there are just 16 across the U.S.), if you forget to plug in the car overnight, or there’s a power outage or some other problem, you’re out of luck. If I had been almost anywhere else in the country, or decided to head north rather than south on Highway 1—or if I’d gotten lost—I would have been stuck by the side of the road.
The charging issue is largely a problem of infrastructure. But the biggest technological issue remains the cost of the battery. It’s the cost that limits the capacity on the Model S and keeps 265-mile-range electric cars out of the hands of most people.
The day before my drive, I toured Tesla’s R&D lab in the hills behind Stanford University. The company’s chief technology officer, JB Straubel, showed me versions of Tesla’s Roadster, its first car, and a Model S with everything removed but the frames, wheels, and the electrical propulsion system (which includes the battery, the motor, and the electronics that control them). It was a stark look at how far the company’s come. In the Roadster, the bulky battery takes up the back third of the car. The Model S’s battery and motor seem to have disappeared. Even though the battery stores far more energy, it’s more compact: it’s now a flat slab that sits inconspicuously between the wheels and serves as part of the vehicle’s frame. What’s not obvious is that the cost of the battery, per kilowatt-hour, has also been cut in half.
Straubel pointed to the wide variety of lithium-ion battery cells—the parts of a battery pack that actually store energy—that the company is testing. This included a row of small cylindrical cells about the size of AA batteries—the kind Tesla uses in the Model S.

Battery packing: The battery pack in the Model S is flat and part of the frame that supports the car—the metal case provides structural support.
Tesla’s choice of these small lithium-ion batteries is, arguably, one of its most important strategic gambles. Established automakers have chosen larger battery cells—they make engineering a battery pack simpler, since you need fewer of them. But the larger cells, because they contain more energy, are also more dangerous. So automakers use less energy-dense battery materials that are more resistant to catching fire. Trying to offset the lower energy density, automakers chose flat cells because they pack together more densely, but such cells cost more to manufacture.
By choosing smaller, cylindrical cells, Tesla saved on manufacturing costs—their costs have been driven down by economies of scale for the laptop industry, for which the cells were developed. Tesla could also use the most energy-dense battery materials available, in part because smaller cells are inherently less dangerous. And better energy density reduces materials costs. This approach meant Tesla had to develop a way to wire together many thousands of separate cells, compared to several hundred of the larger cells. Straubel also invented a liquid cooling system that snakes between the cells and can remove heat so quickly that a problem with one cell doesn’t spread to the others.
Choosing the smaller, cylindrical cells also gave Tesla more flexibility in packaging the cells. Large, flat cells will deform in a collision and possibly catch fire, so other automakers have had to find places within the car where the battery would be out of the way in a crash. That meant using up some passenger or cargo space. Tesla says it has passed its crash tests without its cells deforming or coolant leaking.
By most estimates, the battery for the Model S that I drove should cost between $42,500 and $55,250, or half the cost of the car. But Straubel indicated that it is already much lower. “They’re way less than half, actually,” he says. “Less than a quarter in most cases.” Straubel says more can be done to lower battery costs. He’s working with cell and materials suppliers to increase energy density more, and he’s changing the shape of the cells in ways that make manufacturing them easier.
Other automakers are taking notice. Dan Akerson, GM’s CEO, has reportedly created a task force to study Tesla. Brett Smith, co-director of manufacturing, engineering, and technology at the Ann-Arbor-based nonprofit Center for Automotive Research, says Tesla has “gone from being the quirky little media darling to being something that is definitely making people in the industry think.”
After recharging at the Gilroy supercharging station, I sped along the highway back toward San Francisco, feeling relieved that I’d been within range of the charging station. As I moved effortlessly through traffic, I couldn’t help feel that electric vehicles are the future, and that Tesla’s strides in batteries and supercharging could bring that future here sooner that I’d thought.
By Kevin Bullis
http://www.technologyreview.com/news/516961/how-tesla-is-driving-electric-car-innovation/
Kommentare
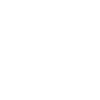