
The fully automated mine has long since passed the days of concept and evolved into a reality. If the industry is to survive and grow, on this planet and elsewhere, total automation of many of the processes is the way forward.
According to professor of mining engineering at the University of British Columbia, John Meech, autonomous vehicle operations can help increase productivity by between 15 to 20 per cent, and truck uptimes by up to a fifth, with Rio Tinto automated fleets recording a 12 per cent production increase compared to manned vehicles.
Rio Tinto, BHP, Roy Hill, and Fortescue are making massive strides forward in implementing autonomous haulage systems in the Pilbara, forging a new place for the technology, combining them with manned operations; particularly in terms of Rio's Mine of the Future program and BHP's automated operations centre, both located in Perth.
Hitachi is also trialling its autonomous vehicle systems at the Meandu coal mine in Queensland.
Total automation has also taken another angle with Vale, in Brazil, looking to go completely truckless by using mobile conveyor belts.
In economic and safety terms automation is the way forward, as it allows for predictable and repeatable operations, which in turn allows for greater confidence in analysis and throughput.
Currently the industry is in the early days of this evolution, and working through the teething problems typically associated with any new technology.
One stand out factor for automation is that it was pegged as being safer than many current techniques, as by removing the man from the operation you remove them from the risk.
But what happens if the risk comes to them?
Automation, like any system on the mine, is not infallible.
An Australian first?
A recent incident in Western Australia at BHP's Jimblebar iron ore mine saw what may be the first serious collision incident involving an autonomous vehicle, after one collided with a manned water cart on the West Australian mine site.
According to the WA Department of Mines and Petroleum, the control room operator had programmed the autonomous haul truck to turn right at a pre-defined intersection and carry out a loop so it could be repositioned underneath an excavator on the pit floor.
While the intersection and loop existed in the control system, it was not physically signposted or marked on the ground to notify worker operated vehicles.
"A manned water cart was travelling in the opposite direction when the autonomous truck was about to turn right, the water cart driver was not aware of the autonomous truck's pre-assigned path and - on recognising it - tried to take evasive action," the DMP report states.
"On detecting the water cart in its assigned path of travel, the autonomous truck's speed (about 40 kilometres per hour) and response time meant it could not prevent the collision.
"The two vehicles collided, resulting in significant damage to the autonomous truck; the water cart driver received minor injuries."
It went on to state that change management processes for planning and assigning roads in the control system were inadequate, and that while an awareness system had been installed in the water cart to allow drivers to monitor autonomous trucks' paths at the time of the collision the water cart driver was not aware of the intended actions of the autonomous truck.
BHP confirmed the incident, telling Australian Mining that "in August 2014, a manned water cart and an autonomous truck collided at BHP Billiton Iron Ore's Autonomous Haulage Production Trial at Jimblebar.
"No one was injured as a result of the incident.
"A thorough investigation into the incident has been conducted and measures have been implemented to prevent the incident from occurring again."
The spokesperson added that this one-off incident has not dampened the miner's push into automation, stating that "autonomous operations at Jimblebar are ongoing", although they did not define the measures implemented to ensure a similar incident doesn't re-occur.
The DMP went on to call for the elimination, or at the very least mitigation, of manned activities within autonomous mining areas.
It called for greater training of workers in their interactions with autonomous vehicles, an aspect of future mining that is likely to become more prevalent in day to day operations as automated vehicle become a common feature on site.
According to a number of experts this while this appears to be the first major incident in Australia - with the understanding that a similar incident may have occurred at Coldeco's mines in Chile - it is unlikely to be the last.
The first of many?
"No technology is 100 per cent, and it's unrealistic to expect it to be," Toby Walsh, a professor in artificial intelligence at the University of New South Wales, and NICTA, told Australian Mining.
"However it is worth pointing out that when it comes to incidents between fully autonomous and manned vehicles - such as those seen in the trials carried out by Google - most accidents are associated with human error," Walsh said.
Senior visiting researcher in artificial intelligence regulation at Australian National University, Gary Lea agreed.
"In terms of operations, if things do go wrong people instinctively blame machines, but statistically humans are the weak link in the chain," Lea told Australian Mining.
Although when it comes to implementing the technology, Australia may have an edge compared to other nations due to the large open areas away from communities, which allow for a more controlled environment, at least in the Pilbara.
Automation integration
Speaking to Rio Tinto's head of technology and innovation, Greg Lilleyman, he explained that automation needs a strong human backing to be effective.
"A well run mine that implements automation becomes a well run mine that is automated, while a poorly run mine that implements automation simply becomes a poorly run mine that has automation," Lilleyman told Australian Mining.
"Automation of the various processes of a mine helps to add incremental improvements, but if you don't have that strong management team behind it, and the talented and skilled workers to implement it correctly and makes the best of the technology then it won't add much to an operation."
Automation is here to stay, and the industry must prepare for the mix of autonomous and manned machinery on site, and how it best accentuates managed change, and prepare workers for this shift.
"The real issue is how do we educate people for what is going to be a situation across the board," Lea said.
"Australia and the world is on the cusp of a new but very different industrial revolution and it is important that we are planning now to ensure our economy does not get left behind," David Tuffley, a lecturer in applied ethics and socio-technical studies at the School of ICT at Griffith University, stated.
"When it comes to this specific incident it is a question of signage, and looking at the human factors which need more warning than the automated systems, and ensuring changes - such as the one here - are verified on the ground in these mixed environments," Lea explained, with Walsh adding that the focus should be on addressing the fear that automation and robots will take peoples' jobs.
"People need to focus on upskilling, and keeping on top of technological change and work with it rather than just being replaced," Walsh said.
"Technological developments also create new jobs, and importantly for the industry, it can also make previously unviable mines viable.
"People need to ask: What are the jobs of the future?"
AI imminent?
As automation develops it will change the face of mining, its productivity, and future efficiency, as well as existing roles on site
But what risks do fully 'smart' machines and artificial intelligence pose?
Many have focused on the potential existential risk and what it means to humanity in the future, with throwaway references to the film Terminator's 'Skynet' as a future threat.
Lea explained that AI may pose a risk, if done poorly, but as we develop artificial intelligence it has to be done well, and that safety and ethical issues will be front and centre in design and research, so there will be the embedding of ethics in robotic system development.
Professor emeritus, and former professor of robotics at MIT, Rodney Brooks, also dismissed the likelihood of AI posing a threat to humanity.
"People have made super-intelligent robots to be the equivalent to magic that suddenly appears, and once you have magic, you can make any argument you want. No technology is suddenly magic and suddenly overpowering," Brooks told Australian Mining.
"You take it step by step and along the way, you make it so it can't make stupid decisions. It's asinine.
"It's just like you could build super-dangerous trains, but no, we don't have them, because if we find something dangerous about the trains, we regulate. We change what we do."
Walsh added, "computers aren't sentient".
"Trucks aren't going to wake up and suddenly be bored of driving dirt around the mine; there's no desire to take over the world."
The fact remains that as automation evolves on site, so too the regulation which governs it.
"Automation needs to be more regulated," Walsh stated," Australia currently has very stringent OH&S laws but they can't cover new technology like this comprehensively yet."
Lea added: "We are seeing AI get to an eventual situation where systems will be developed in a way that tasks can be done in a way you can't predict all the states it will take in carrying out its role."
"Due to this the law will have to evolve, most likely strict liability for workcover needs to be expanded, or potentially bring in a no fault liability in incidents related to autonomous vehicles.
"In the longer term - in the case of fatalities - criminal liability related to the programming."
Mining is evolving, but the regulations pertaining to safety on site need to evolve in line with these technological developments to ensure workers are not exposed to risks, and operations can achieve that dream of a zero harm mine.
Kommentare
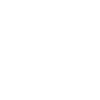