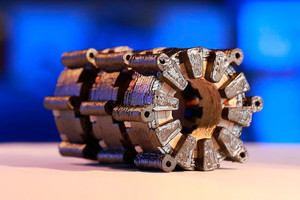
Drucken statt wickeln: Elektrotechnikern der TU Chemnitz ist es gelungen, einen Motor per 3D-Druck herzustellen – als Multimaterial-Mix aus Eisen, Kupfer und Keramik.
Schicht um Schicht trägt der Automat metallische und keramische Pasten auf, bringt sie per Extrusionsverfahren in Form und sintert sie schließlich mikrometergenau zu einem festen Gefüge. Was Elektrotechnik-Forschern an der der Professur für Elektrische Energiewandlungssysteme und Antriebe an der Technischen Universität Chemnitz – weltweit erstmalig – demonstrieren, könnte den Bau elektrischer Motoren revolutionieren: Hier entstehen nahezu komplette Antriebe per industriellem 3D-Druck. „Auf der Hannover Messe 2018 stellen wir diese Weltneuheit erstmalig vor“, freut sich Prof. Dr. Ralf Werner, Inhaber der Professur.
Seine wissenschaftlichen Mitarbeiter Johannes Rudolph und Fabian Lorenz hatten bereits im vergangenen Jahr eine 3D-gedruckte Spule vorgestellt, die Temperaturen von über 300 °C standhalten kann. Inzwischen ist es ihnen mit einem selbstentwickelten 3D-Multimaterial-Druckverfahren gelungen, alle wichtigen Komponenten einer elektrischen Maschine in einem Druckvorgang zu fertigen. Dazu zählen die elektrischen Leiter aus Kupfer, die zusammen mit Eisen und eisenhaltigen Legierungen die magnetischen Felder erzeugen und ausrichten. Das funktioniert allerdings nur, wenn die Leiter untereinander und gegen die als Magnetkreis bezeichneten Teile aus Eisen zuverlässig isoliert sind. Also drucken die Wissenschaftler die keramische Isolierung gleich mit.
Im Labor: Johannes Rudolph überwacht den 3D-Multimaterialdruck eines E-Motors, bei dem erstmals Kupfer, Keramik und Eisen gleichzeitig in einem Druckprozess zum Einsatz kommen. Links sind die Rotoren zu erkennen, rechts der Stator. Kopflos: Diese Statoren einer dreiphasigen, wickelkopflosen Reluktanzmaschine stammen aus einem Multimaterial-3D-Drucker. Entwicklungsschritte des 3D-Drucks: Kupferwicklung, keramisch isolierte Spule, Spule mit separat gedrucktem Eisenkern und elektrische Maschine (von links).
„Seit zweieinhalb Jahren arbeiten wir daran, die Grenze der Einsatztemperatur von elektrischen Maschinen deutlich nach oben zu verschieben“, erklärt Werner. Der Durchbruch gelang mit speziellen Keramiken, die gegenüber konventionellen, polymerbasierten Isolationsmaterialien eine weitaus höhere Temperaturbeständigkeit aufweisen. „Konventionelle Isolationssysteme haben eine zulässige Wicklungstemperatur von maximal 220 °C. „Durch den Einsatz der Keramiken können wir diese deutlich überschreiten“, erläutert der Professor. Bei den gedruckten Motoren würden erst die ferromagnetischen Eigenschaften des Eisens die Einsatztemperatur elektrischer Maschinen begrenzen. Diese Grenze „liegt derzeit bei circa 700 °C“.
Das keramische Isolationsmaterial ist jedoch nicht nur temperaturbeständiger, sondern kann Wärme auch besser ableiten. Verlustwärme in den Leitern lässt sich also effizienter abführen. Dadurch ist es möglich, die Leistungsdichte elektrischer Maschinen zu erhöhen – was ein weiteres wichtiges Ziel der Chemnitzer war. „Trotz einer prozessbedingten, etwas verminderten elektrischen Leitfähigkeit des Kupfers, lässt sich mit unserem Verfahren in speziellen Anwendungsfällen der Wirkungsgrad durch deutliches Reduzieren der Wicklungstemperatur verbessern“, ergänzt Lorenz.
Grundlage des Verfahrens, das die Chemnitzer Forscher nun zur Marktreife weiterentwickeln wollen, ist die schichtweise Extrusion hochviskoser Pasten. Diese enthalten Partikel der gewünschten Materialien wie Eisen, Kupfer oder Keramik und speziell zugeschnittene Bindemittel. Die für den Multimaterialdruck notwendige Präzision beim Dosieren der Pasten zu erreichen, ist nicht trivial. Hier arbeiten die Forscher eng mit der Firma ViscoTec Pumpen- und Dosiertechnik in Töging am Inn zusammen.
„Der im Chemnitzer Uni-Labor gedruckte Motor stellt einen Durchbruch dar und ist gleichzeitig der Proof of Principle – also der Machbarkeitsnachweis – für unsere Technologie“, versichert Rudolph, der das Verfahren maßgeblich mitentwickelt hat und zusammen mit Lorenz eine Ausgründung aus der Universität vorbereitet. Den aktuellen Stand ihrer Forschung werden die Wissenschaftler vom 23. bis 27. April 2018 auf der Hannover Messe am Gemeinschaftsstand „Forschung für die Zukunft“ in Halle 2, Stand A38, präsentieren. Dort hoffen Rudolph und Lorenz weitere Interessenten für ihr neues 3D-Multimaterialdruck-Verfahren gewinnen zu können.
Quelle: Elektropraxis – next-mobility.news
Kommentare
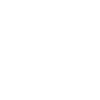